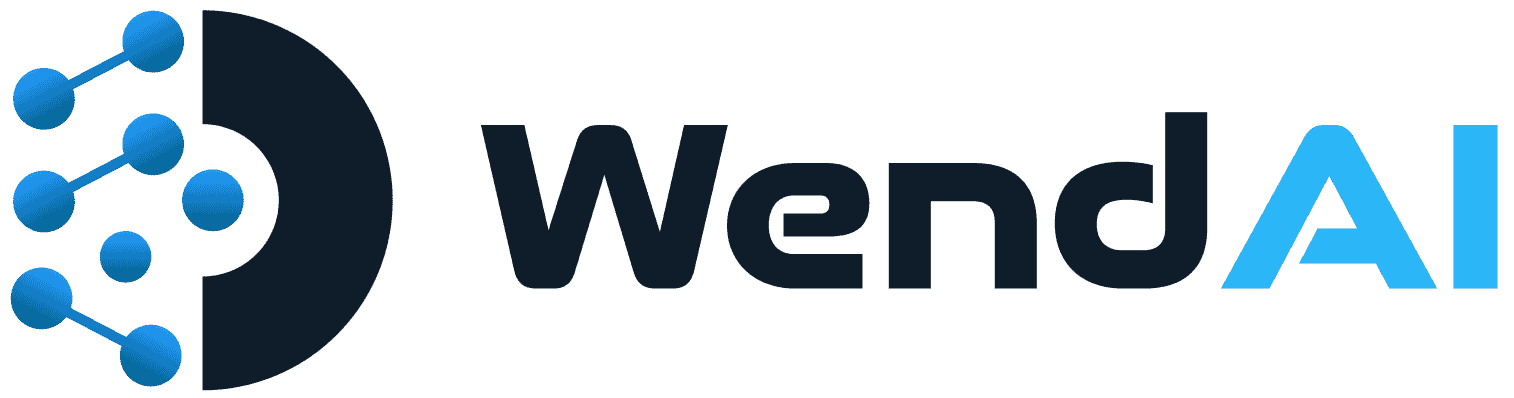
AI that turns everyday tasks into automated workflows.
From reading files and emails to triggering actions, WendAI automates the work that slows you down.
Workflows fully automated from input to action
Data accuracy across mixed formats
Smarter Than Just Parsing
Understands, Not Just Extracts
- WendAI goes beyond surface-level data, grasping context, priorities, and intent to make smarter decisions.
- It interprets contextual cues to apply business logic—like calculating timelines or recognizing tax rules—without needing hardcoded instructions.
- This reduces manual effort, prevents errors, and speeds up decision-making across your workflows.
Human-in-the-Loop by Design
Learns as You Work
Built Around Your Processes
Understands, Not Just Extracts
WendAI goes beyond surface-level data, grasping context, priorities, and intent to make smarter decisions.
It interprets contextual cues to apply business logic—like calculating timelines or recognizing tax rules—without needing hardcoded instructions.
This reduces manual effort, prevents errors, and speeds up decision-making across your workflows.
Human-in-the-Loop by Design
When in doubt, WendAI checks with you, keeping humans in control while reducing errors.
It pauses automation when confidence is low, flags uncertain fields, and asks for your input—ensuring accuracy without breaking the flow.
This builds trust, improves reliability, and keeps automation aligned with human judgment.
Learns as You Work
Every interaction makes WendAI smarter, continuously refining how your workflows run.
It remembers your corrections—like preferred field formats or vendor-specific variations—and improves future results automatically.
This leads to faster processing, fewer repetitive edits, and a system that adapts to your way of working.
Built Around Your Processes
No rigid templates. WendAI moulds to your existing workflows—fully customisable and enterprise-ready.
It adapts to your rules, layouts, and naming conventions—whether you're automating invoice reviews or quality checks.
This means faster adoption, minimal change management, and automation that truly fits your business.
WendAI for Supply Chain & Logistics

Quotations
Extract pricing and terms instantly for faster freight quote comparisons

Invoices
Capture key billing details and streamline accounts payable processing

Bills of Lading (BOL)
Read and record shipping terms, cargo data, and consignee info

Consignment Notes
Digitize and validate shipping details for transparent tracking

Packing Declarations
Automate data extraction to speed up customs clearance

Certificates of Analysis
Verify and archive quality assurance data without manual checks
The WendAI Advantage
Built for real-world operations, WendAI goes beyond data parsing to deliver smart, scalable workflow automation - designed to fit your business, not force you to change it




Why Teams Love WendAI
Real teams. Real workflows. Real results. Discover how WendAI transforms everyday operations across finance, logistics, retail, and procurement.
Easily Fits Into Your Tech Stack
WendAI seamlessly integrates with all the popular apps and platforms. Effortlessly export your data to Excel.
From our blog
FAQs
What exactly does WendAI automate?
WendAI automates repetitive tasks across your workflows—like reading emails, processing purchase orders, extracting key data from PDFs, and triggering follow-up actions. It's built for intelligent document processing, not just file reading.
Is WendAI just a document parser or PDF tool?
No. WendAI does far more than parse PDFs. It uses OCR with AI to understand content, extract context, and automate workflows—from approving freight quotes to processing invoices or verifying planograms.
Can WendAI handle logistics documents like the bill of lading?
Yes. WendAI is designed to read and process logistics documents including the bill of lading form, customs declaration, and related shipping paperwork—saving teams hours of manual work.
How does WendAI support finance workflows like invoicing or accounts payable?
WendAI streamlines tasks like invoice capture, matching quotes to invoices, and managing accounts payable and receivable—all within a single flow. It works well as a best-in-class invoice automation software for teams looking to move fast and reduce errors.
Can WendAI handle both purchase orders and proforma invoices?
Yes. Whether it’s a standard PO or a proforma invoice, WendAI can identify, extract, and route the relevant data to the right system—ideal for teams using purchase order software or managing vendor flows at scale.
Does WendAI integrate with our existing business process tools?
Absolutely. WendAI complements your current setup—whether you're using ERP, CRM, or business process management tools. It's a flexible layer of AI-powered business process automation, not a system overhaul.
What makes WendAI different from traditional business automation software?
Unlike static automation tools, WendAI uses AI to adapt, learn from human input, and improve over time. It's built for modern business automation where workflows aren't always linear and data comes in many forms.
How secure is WendAI for handling sensitive business documents?
WendAI follows strict security protocols including encryption and role-based access controls, making it safe for processing financial data, logistics documents, and other confidential records.